Solder or Crimp
Connectors are available in several types - screw-on, screw terminal, crimp, or solder - the last two being the most common for the majority of signals. Crimp type connectors offer significant convenience.
They can often be assembled in minutes with the right tools, providing a quality connection. That time savings can be significant, leading to savings in hours and cost on a project.
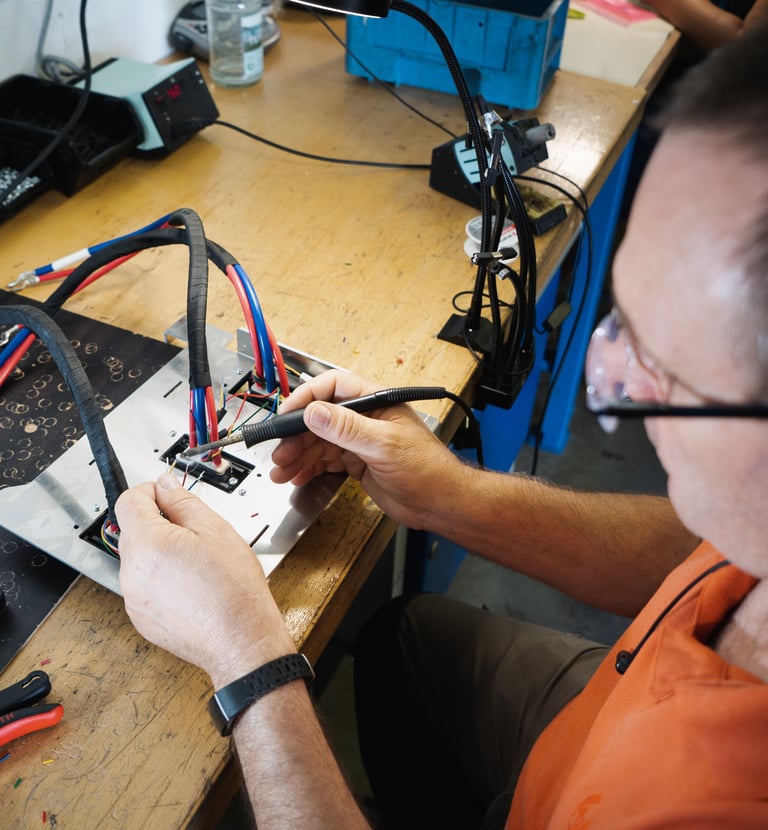
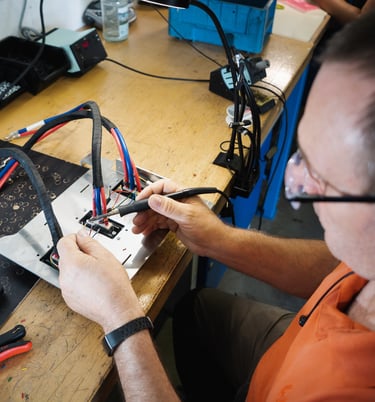

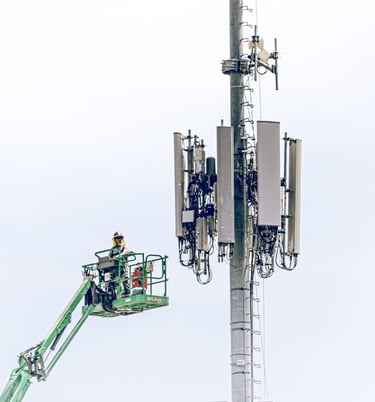
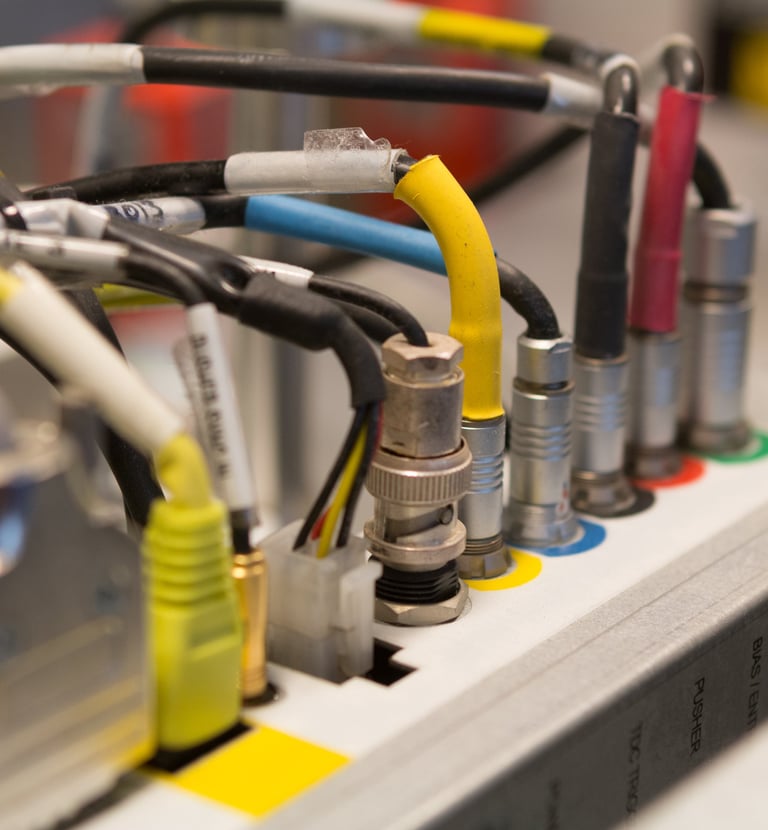
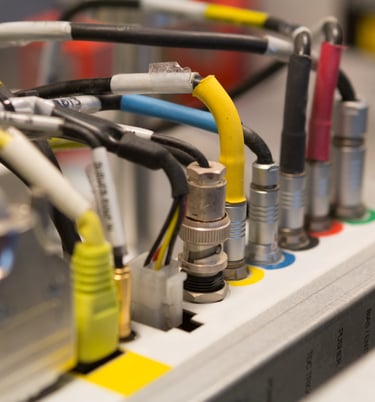
What Drives the Decision to Crimp or Solder a Connector?
Application requirements: The specific needs and requirements of the application, such as the type of signal being transmitted, the environment in which the connector will be used, and the level of reliability required, will often play a significant role in determining whether crimping or soldering is the preferred method.
Time and labor constraints: Crimping is generally faster and requires fewer tools and materials than soldering, so if time and labor are a concern, crimping may be the preferred option.
Skill level and expertise: Soldering requires a higher level of skill and expertise than crimping, so if the personnel performing the installation are inexperienced or untrained in soldering, crimping may be a safer and more reliable option.
Cost: The cost of materials and equipment required for crimping or soldering can also be a factor, as crimping tools and connectors are typically less expensive than soldering tools and materials.
Ease of maintenance: If maintenance or repair of the connector will be required in the future, crimped connectors can be easier to replace or re-crimp than soldered connectors.
Consider the environment: If it is fairly well climate controlled, with little or no chance of frequent movement, crimp connectors can be quite effective provided they are assembled with the proper tools. In more harsh environments, soldered connectors should be used to provide more reliable connections.
Power (current or RF) and frequency: Higher power connections will be subjected to more stress from heating due to higher inherent resistance of crimped connections and thus more prone to early failure. Higher frequency signals, whether RF or not, are significantly affected by any increased resistance which could occur with crimped connectors, so soldered connections are recommended.
Ultimately, soldered connections are better suited for the majority of applications. Crimped connections can be very reliable, as well as time and cost savers.
Advantages of Soldering
Improved electrical performance: Soldering the center pin ensures a secure and stable electrical connection, which can improve the electrical performance of the connector. This can result in better signal transmission and reduced signal loss.
Increased mechanical stability: Soldering the center pin can also provide increased mechanical stability, as it helps to prevent the pin from becoming loose or detached from the connector. This can be particularly important in high-vibration environments.
Enhanced durability: Soldering the center pin can also help to increase the durability of the connector, as it can help to prevent damage to the pin from repeated use or rough handling.
Overall, soldering the center pin on a connector is generally recommended for applications where reliable, high-performance signal transmission is critical.
Advantages of Crimping
Ease of installation: Crimping the center pin can be a faster and easier installation method than soldering, as it requires fewer tools and can be completed more quickly.
Consistency: Crimping can provide a more consistent connection, as the crimping tool applies the same amount of pressure and compression to each connector, ensuring a uniform connection.
Flexibility: Crimping can be a more flexible option, as it allows for the center pin to be replaced or re-crimped if necessary. This can be particularly useful in applications where connectors may need to be frequently disconnected and reconnected.
Cost: Crimping can also be a more cost-effective option, as crimping tools and connectors are typically less expensive than soldering tools and materials.
Overall, crimping the center pin on a connector can be a good option for applications where ease of installation, consistency, flexibility, and cost are important considerations. However, it may not be the best option for applications where extreme reliability and high-performance signal transmission are critical, in which case soldering may be the better choice
Disadvantages of Soldering
Difficulties in achieving a proper connection: Soldering requires more skill and precision than crimping, so achieving a proper connection can be more challenging, particularly for inexperienced or untrained personnel.
Increased time and labor requirements: Soldering can be more time-consuming and labor-intensive than crimping, as it requires the use of additional tools, materials, and a heat source.
Potential for overheating: Overheating the connector during soldering can cause damage to the insulation, which can lead to reduced electrical performance and potentially even equipment failure.
Limited flexibility: Once soldered, the center pin cannot be easily removed or re-soldered if necessary, which can limit the flexibility and versatility of the connector.
Overall, the choice between crimping or soldering the center pin on an N Male LMR400 connector will depend on the specific needs and requirements of the application. While soldering can offer advantages such as improved electrical performance and increased mechanical stability, it may not be suitable for applications where ease of installation, flexibility, or cost-effectiveness are more critical considerations.
Disadvantages of Crimping
Reduced electrical performance: Crimping can result in a less secure and stable electrical connection compared to soldering, which can result in increased signal loss and reduced electrical performance.
Limited durability: Crimped connections may not be as durable as soldered connections, as the crimping process can create stress points on the connector, potentially leading to fatigue or failure over time.
Tooling requirements: Crimping requires specialized crimping tools, which can be expensive to purchase and maintain.
Potential for error: Incorrectly crimped connectors may not provide a reliable connection, which can lead to performance issues or even equipment failure.
Overall, the choice between crimping or soldering the center pin on a connector will depend on the specific needs and requirements of the application. While crimping can offer advantages such as ease of installation and cost-effectiveness, it may not be suitable for applications where high-performance signal transmission and extreme reliability are critical.